位于东京以北约100公里的宇都宫市,是佳能EF镜头以及包括视频摄像机、广播器材和投影机在内等产品镜头的工厂所在地。
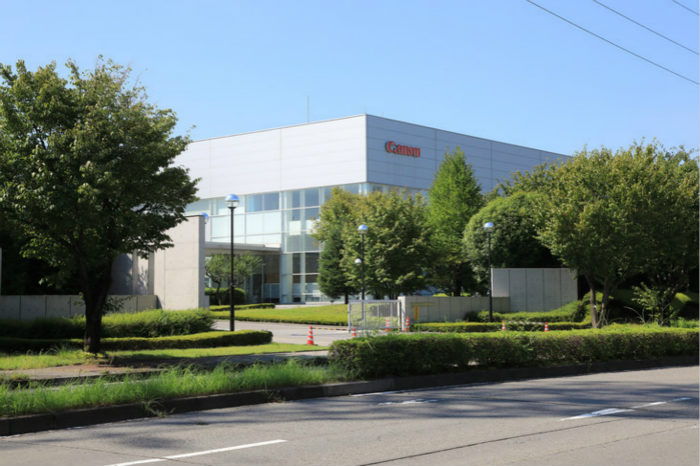
这里是佳能光学研究的大本营,主要研究各种光学镜头,并给佳能的其他工厂提供技术支援。为了能够制造出理想的镜头,佳能工厂不仅充分利用长期积累的光学技术进行生产,还会通过自研装置完成镜头的各种精密组装。
在宇都宫工厂的北面,坐落着佳能引以为傲的光学研发中心,佳能所有镜头的开发和设计均在这里完成,然后交于对面的工厂继续完成生产制造环节。
截至2014年,这座工厂负责生产了1亿支EF镜头。而在每一支镜头背后,不仅有现代工艺的改进与革新,更有手工匠人的技艺传承。
据佳能宇都宫工厂相关负责人介绍,所有数码相机EF镜片的诞生,都需要经历球面镜片加工、SWC(亚波长结构镀膜)、组装等多道工序。其中仅球面镜片加工的抛光,便需要进行粗磨、精磨削、取芯、粗抛光、精抛光等一系列繁琐但却必不可少的精细工艺,且每一道工序都有着严格的标准。

特别是在生产镜头最重要的研磨工序,这种标准更为苛刻。通常我们所见到的镜片成品都是晶莹通透的,但他们本来的“真身”是一块有着磨砂视觉效果的玻璃坯,在完成研磨、平滑加工、抛光、中心定位、清洗以及最终的检查环节后,才会呈现出镜片成品的状态。佳能要求镜片表面的粗糙度必须控制在0.8纳米,表面误差精度需要严格控制在0.06mm。如果把一枚镜片放大到鸟巢国家体院馆大小,意味着修建鸟巢的曲面误差不能超过2mm。
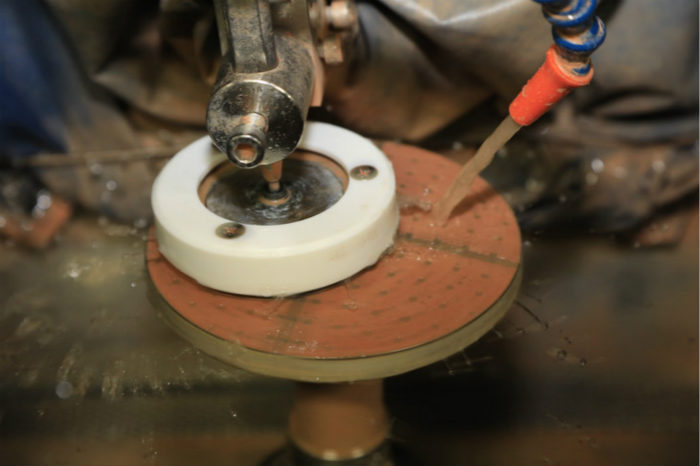
尽管佳能镜片已经实现了自动化生产,但为了打造出高精度的镜片,其所使用的磨具无法进行机器加工,必须由具备熟练技能的工匠来制作手工磨具。
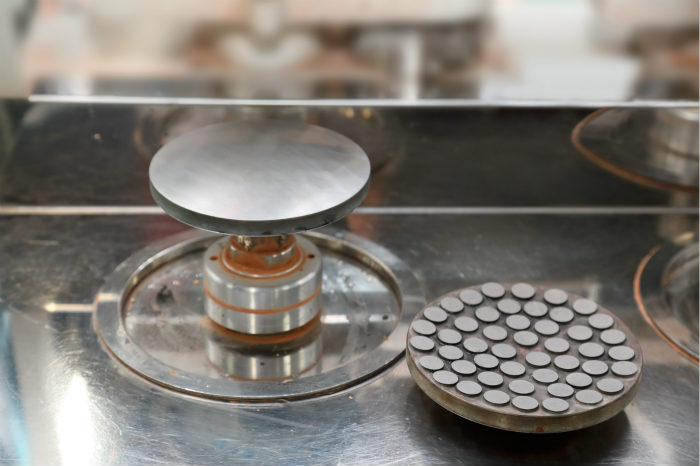
佳能镜片抛光高级技师斋藤敏夫(Toshio Saito)便是这样一位独特的匠人。
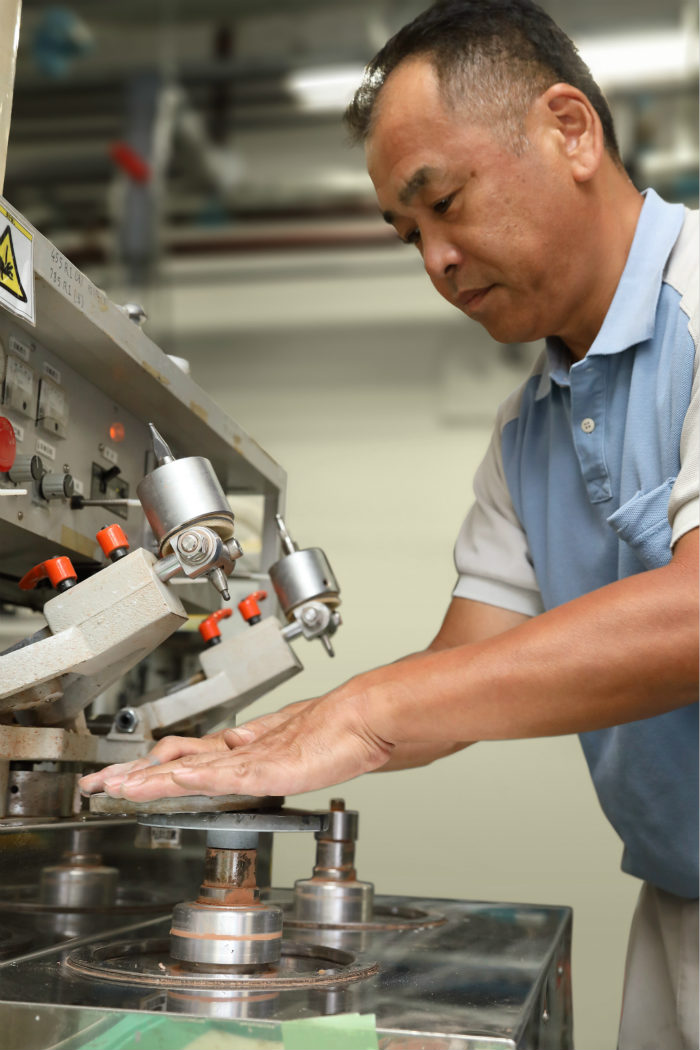
他于1981年加入宇都宫工厂,入职37年来一直致力于光学镜片的加工工艺,被评为S级匠人(一种相当高级别的匠人)。目前该工厂使用的很多磨具都是斋藤敏夫亲手制作而成,要控制好磨具的精度需要倚赖其多年训练而来的经验,以及手上一种特殊的皮肤感觉。只要用手摸一摸,他就能判定出磨具是否达到了应有的标准。
目前他不仅负责超高精度镜片的加工规划阶段工作,也承担着监管下一代工厂工人的培训工作。
“对于现在的工作,我感到很荣幸。正是经过无数次的抛光、镜片的研磨才有了现在的我。”斋藤敏夫说,他很高兴看到,佳能广播器材的研磨工作交给新一代的年轻匠人来完成,也会继续培养更多的匠人出来。
另一位负责EF镜头组装车间管理的Miyoko kobanaWa也是一位S级匠人。她比Toshio Saito晚两年进入佳能,在手工组装镜头方面有着丰富的经验。
一枚佳能镜头,特别是一些红圈高端镜头会内置很多镜片和传动装置,每一个零部件一旦出现轻微偏移便可能影响到镜头整体的光学性能。所以有些镜头可以依靠机器完成,但一些高端镜头仍然需要像Miyoko kobanaWa这样有经验的匠人手工组装完成,还有一些则是机器与人工结合完成。
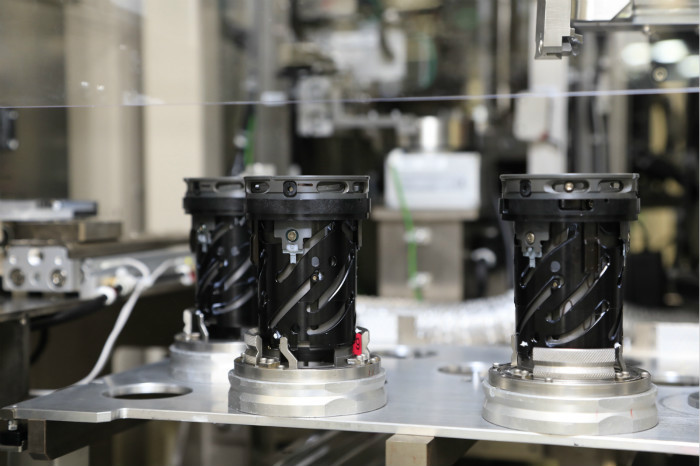
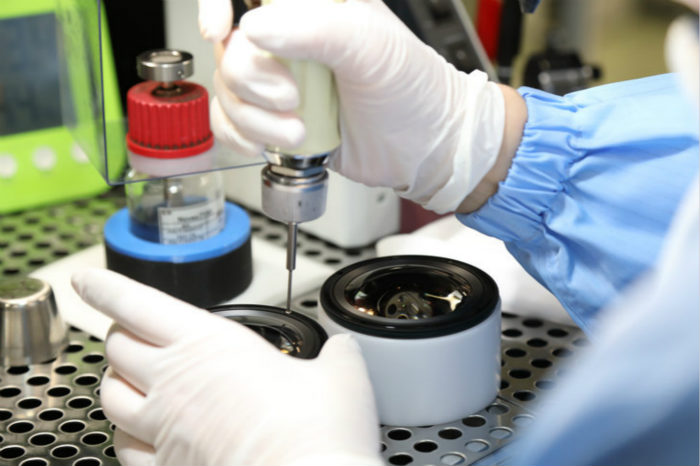
佳能还首次向媒体展示了SWC(亚波长结构镀膜)工艺。如果对玻璃产品不做加工,通常有光线穿透时会出现反射情况。为了解决上述问题,常见工艺是添加一层很薄的薄膜,但在光线较强时很容易出现重影的状态,即“鬼影”现象。
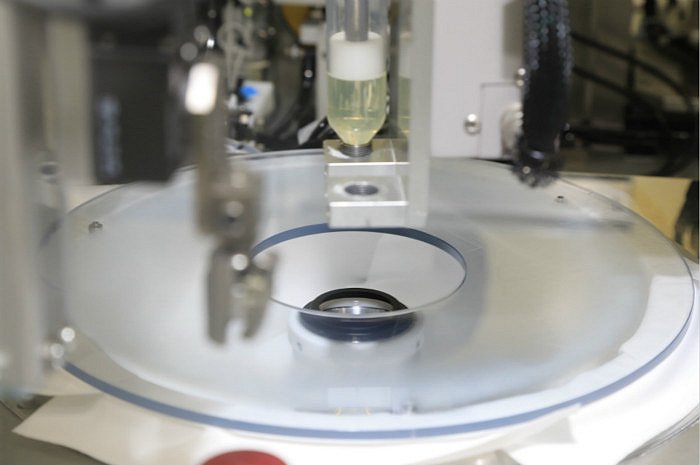
佳能则想到通过逐渐改变折射率来避免光线反射,具体的做法便是在严格把控水温的情况下,经由材料涂布、烧成等加工工序,形成一层完美的结晶镀膜表面,使光线更平稳过渡到玻璃镜片的表面。
由于上述工艺具有一定难度,目前只是在佳能的高端镜头上采用了SWC。但佳能工厂也在不断提升这种工艺的合格率,希望应用在更多的镜片上。